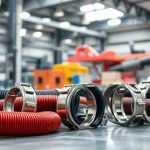
Understanding Clamp on Hoses
In industries ranging from automotive to manufacturing, the importance of reliable fluid management cannot be overstated. A key component of effective fluid transfer systems is the clamp on hose, which serves as both a connector and a stabilizer for hoses used in various applications. Understanding clamp on hoses, their types, and applications is essential for choosing the right equipment for your specific needs.
What is a Clamp on Hose?
A clamp on hose is a type of flexible tubing that is equipped with a clamping mechanism to secure the hose in place. These hoses can be made from various materials, including rubber, plastic, and metal, to suit different applications. The clamping system is designed to create a tight seal between the hose and any fittings or connections, preventing leaks and ensuring the efficient transfer of fluids or gases.
Types of Clamp on Hoses
Clamp on hoses can be categorized into several types based on their construction, material, and intended use. Here are some common types:
- Worm Gear Clamps: These clamps feature a stainless steel band that can be tightened or loosened with a screw mechanism, making them adjustable for various hose sizes.
- T-Bolt Clamps: Known for their strength, T-bolt clamps provide a secure fit and are typically used in high-pressure applications, such as heavy machinery and industrial settings.
- Spring Clamps: Designed for quick installation and removal, spring clamps automatically adjust to the hose diameter and are ideal for temporary connections.
- Constant Tension Clamps: These clamps maintain consistent pressure on the hose regardless of thermal expansion or contraction, making them suitable for high-temperature applications.
Applications of Clamp on Hoses
Clamp on hoses are utilized across various industries and applications including:
- Automotive: Used for coolant, fuel, and air intake lines, ensuring a secure connection that withstands vibrations and temperature changes.
- Aerospace: Lightweight and high-strength clamp on hoses are crucial for fuel and hydraulic systems in aircraft.
- Manufacturing: In production processes, these hoses facilitate the transfer of liquids, chemicals, and gases with precision and reliability.
- Marine: Durable materials used in clamp on hoses that resist corrosion are key for high-pressure water systems in boats and ships.
Advantages of Using Clamp on Hoses
Durability and Reliability
One of the primary advantages of clamp on hoses is their durability. They are engineered to handle extreme temperatures, corrosive fluids, and high-pressure environments. Properly installed clamp on hoses can last for years, reducing the frequency of replacements and potential downtimes in operations.
Efficiency in Fluid Management
Clamp on hoses ensure a tight seal that minimizes leaks, contributing to efficient fluid transfer systems. This efficiency is vital in applications where even minor leaks can lead to significant losses or safety issues. Additionally, the proper choice of hose and clamp can enhance the flow rate, optimizing operational performance.
Ease of Installation and Maintenance
Another significant benefit is the straightforward installation process of clamp on hoses. Most types can be installed with minimal tools and expertise, allowing for quick replacements or adjustments. Regular maintenance is also simplified, as professionals can easily access and inspect these systems without the need for specialized equipment.
Choosing the Right Clamp on Hose for Your Needs
Size and Fit Considerations
Choosing the right size of a clamp on hose is critical to ensuring a secure fit. Measurement should include the inner diameter of the hose as well as the size of the fitting it will connect to. The clamp itself should be able to adjust adequately to accommodate any variations in these dimensions, ensuring a tight seal.
Material Options for Different Environments
Different environments require various materials for clamp on hoses. For instance, rubber hoses are often flexible and suitable for low-pressure applications, while metal hoses might be necessary for high-pressure or high-temperature environments. Users must consider chemical compatibility as well—certain materials may degrade when in contact with specific fluids.
Assessing Performance Specifications
Before making a decision on a clamp on hose, it’s essential to review performance specifications: temperature ratings, pressure limits, and flow characteristics. These metrics will guide users to select a product that meets the demands of their specific application, ensuring both safety and efficiency.
Common Challenges with Clamp on Hoses
Identifying Hose Leaks
Despite their reliability, users may occasionally face issues with hose leaks. Regular inspection is essential; this may involve visual checks and pressure testing. Understanding the common signs of leaks—like fluid pooling, discoloration, or unusual pressure drops—can help in early diagnosis.
Dealing with Material Compatibility
Material compatibility stands out as a prevalent concern when selecting a clamp on hose. If the hose material is not chemically compatible with the fluid, it can lead to degradation and eventual failure. Researching the fluid’s properties and checking manufacturer’s specifications prevents complications.
Preventing Damage in High-Pressure Systems
High-pressure systems place greater demands on hoses and clamps. To prevent damage, it’s crucial to utilize clamps designed to withstand high pressure and to install them according to the manufacturer’s recommendations. In some cases, reinforcing hoses with additional protective layers or sleeves may be necessary.
Best Practices for Clamp on Hose Installation
Step-by-Step Installation Guide
- Measure the Hose: Ensure the correct length and diameter.
- Prepare the Fitting: Clean any debris or old sealant from the fitting surface.
- Insert the Hose: Push the hose onto the fitting until it’s secured.
- Position the Clamp: Place the clamp over the connection site.
- Tighten the Clamp: Use a screwdriver or wrench to secure the clamp until it’s snug but not over-tightened.
- Check for Leaks: After installation, run the system and check for leaks.
Tools Required for Proper Fitting
Installing clamp on hoses typically requires only a few tools, including:
- Screwdriver (for worm gear clamps)
- Wrench (for T-bolt clamps)
- Hose cutters or scissors (for trimming hoses)
Regular Maintenance Tips and Tricks
Maintenance extends the life of clamp on hoses and prevents issues. Recommendations include:
- Regularly inspect hoses for signs of wear, bulging, or cracking.
- Check clamp tightness periodically, especially after temperature changes.
- Replace hoses or clamps that show any signs of damage.
- Consult manufacturer guidelines for specific maintenance standards.