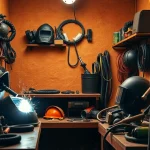
Understanding Welding Supplies
What are Welding Supplies?
Welding supplies encompass a variety of tools, materials, and safety equipment essential for performing welding tasks effectively and safely. These supplies are used in numerous applications, from industrial manufacturing to artisanal crafts, highlighting their versatility. Whether you are a seasoned professional or a DIY enthusiast, understanding the components involved in welding can significantly enhance your efficiency and output. The right selection of welding supplies contributes to successful projects by ensuring quality and safety standards are met.
Types of Welding Supplies Available
Welding supplies can be broadly categorized into several types:
- Welding Equipment: This includes machines like MIG welders, TIG welders, and stick welders, which are essential for different welding processes.
- Consumables: Items such as welding rods, wires, and electrodes that are used up during welding.
- Protective Gear: Essential safety items, including helmets, gloves, jackets, and respirators designed to protect the welder from sparks, heat, and toxic fumes.
- Welding Accessories: Items that support the welding process, such as clamps, magnets, and positioners that help manipulate the workpiece.
- Cleaning and Preparation Tools: Tools like grinders and brushes used to prepare and clean the welding surfaces for optimal results.
Benefits of Quality Welding Gear
Investing in quality welding supplies has both immediate and long-term benefits. The advantages include:
- Enhanced Safety: Quality gear provides better protection, reducing the risk of accidents and health issues associated with welding.
- Improved Efficiency: High-quality tools and materials lead to better weld quality and reduced rework time, maximizing productivity.
- Cost-Effectiveness: Although quality supplies may have a higher upfront cost, their durability and performance can save money in the long run.
- Better Performance: Superior supplies often result in stronger, more reliable welds, which is essential for structural integrity, especially in high-stake applications.
Key Welding Supplies for Every Project
Essential Tools for All Welding Techniques
The specific tools required for welding vary based on the technique employed. However, there are certain essential tools that every welder should have:
- Welding Machines: Whether it’s MIG, TIG, or stick welding, having the right machine is crucial. Consider brands known for their reliability, such as Miller and Lincoln Electric.
- Electrodes and Wires: The choice of consumables impacts the weld’s quality. Ensure you select compatible materials for your welding technique.
- Protective Gear: Every welder should have a quality helmet with appropriate shading, gloves, and protective clothing to handle the job safely.
- Welding Clamps and Magnets: These tools stabilize and position metal workpieces precisely during the welding process, significantly improving accuracy and ease.
- Chipping Hammer and Wire Brush: These are used to clean up slag and spatter from welds, ensuring a neat finish and preparing the surface for further welding.
Safety Equipment in Welding Supplies
Safety should always be the primary concern when welding. The following equipment is essential:
- Welding Helmets: Choose automatic darkening helmets that protect your eyes from bright arcs and sparks while allowing visibility.
- Welding Gloves: Insulated and durable gloves protect your hands from heat and sparks while allowing good dexterity.
- Protective Clothing: Flame-resistant jackets and pants should be worn to protect skin from burns.
- Respirators: These are critical if you are working in an area with poor ventilation, as they help protect against toxic fumes.
- Safety Glasses and Ear Protection: Additional protective gear helps ensure you are fully safeguarded while working.
Choosing the Right Welding Supplies for Your Needs
Selecting the appropriate welding supplies depends on various factors:
- Project Requirements: Assess the specific needs of your project based on material type, thickness, and desired strength of the weld.
- Welding Technique: Choose supplies that align with the welding method you plan to use, whether it be MIG, TIG, or stick.
- Budget: Set a clear budget while keeping in mind the balance between cost and quality. It’s often worth investing more in high-quality gear.
- Brand Reputation: Research and select brands with a track record of reliability and performance, ensuring you choose reputable vendors.
Top Brands for Welding Supplies
Review of Leading Welding Supply Brands
Numerous brands offer quality welding supplies, but some have distinguished themselves in the industry:
- Miller Electric: Known for their reliable welders and accessories, Miller stands out for innovation and quality.
- Lincoln Electric: A historical leader in the welding market, they provide a comprehensive range of equipment suitable for all skill levels.
- ESAB: Renowned for their welding and cutting equipment, ESAB offers tools that cater to both industrial and portable applications.
- Hypertherm: Primarily known for plasma cutting, Hypertherm also provides quality welding supplies.
- Hobart: A solid choice for hobbyists and professionals alike, offering affordable yet reliable welding machines.
Comparison of Features and Prices
When comparing welding brands, consider the following features:
- Ease of Use: Machines that offer intuitive controls tend to be easier to operate, especially for beginners.
- Versatility: Some machines can perform multiple welding processes (e.g., MIG/TIG), which can save investment costs.
- Warranty and Support: Brands that offer robust customer service and warranty can provide peace of mind about your purchase.
- Cost: Prices vary widely. Quality entry-level machines can start around $200, while professional-grade units can exceed $3,000.
Where to Buy Trusted Welding Supplies
Purchasing welding supplies can be done through various avenues:
- Online Retailers: Websites such as Cyberweld and Welders Supply offer a vast range of products with convenient shipping options.
- Local Welding Supply Stores: Visiting a local store allows for hands-on examination of equipment and personalized advice from sales staff.
- Industry Trade Shows: Attending trade shows provides exposure to multiple brands and the opportunity to gain insights and network within the industry.
- Direct from Manufacturers: Some brands allow customers to purchase equipment directly from their websites, often promoting exclusive deals.
Caring for Your Welding Supplies
Maintenance Tips for Longevity
Like any tools, maintaining and caring for welding supplies is crucial for longevity and performance:
- Regular Cleaning: Ensure your welding equipment is cleaned after each use, especially the nozzle and contact tips, to prevent excessive spatter build-up.
- Inspect for Wear: Routinely check consumables and safety gear for any signs of wear or damage, replacing them as needed.
- Store Properly: Gear should be stored in a dry, clean place to prevent rust and damage, especially for metal components.
- Follow Manufacturer Guidelines: Always adhere to maintenance recommendations provided in the operating manuals for optimal care.
Storing Welding Supplies Safely
Proper storage is just as important as maintenance. Here are some tips:
- Organized Storage: Using shelves and bins can help keep your workspace clean and your supplies organized, making it easy to find what you need.
- Temperature Control: Store supplies in a climate-controlled environment to prevent the materials from deteriorating.
- Secure and Lockable Areas: For high-value items, consider secure storage options to prevent theft and unauthorized use.
- Labeling: Clearly label bins and shelves for easy identification and quick access to frequently used items.
When to Replace Your Welding Gear
Replacing welding gear is essential for safety and performance. Here are signs to look out for:
- Visible Damage: If you notice cracks, tears, or other physical damage to protective gear, it’s time to replace it.
- Decreased Performance: When welding machines or tools no longer perform as they did initially—frequent issues could indicate they need replacement.
- Age: Even if gear looks good, consider the manufacturer’s recommended lifespan for safety equipment.
- Outdated Technology: Advances in welding technology may make older tools less efficient, prompting an upgrade.
Investing in Welding Supplies: A Cost-Benefit Analysis
How to Budget for Welding Equipment
Creating a budget for welding supplies involves careful consideration of your immediate needs and future projects. Here are steps to guide you:
- Assess Your Needs: Determine the types of projects you will undertake, which helps prioritize the necessary equipment.
- Research Costs: Investigate the cost of various machines and tools, comparing prices between retailers.
- Plan for Consumables: Regular use of consumables like welding rods and gases should be factored into your budget.
- Consider Financing Options: If necessary, look into financing options for purchasing expensive machinery to manage costs effectively.
Cost-Saving Tips for Buying Welding Supplies
There are several strategies for saving money without compromising on quality:
- Buy in Bulk: Purchasing consumables in larger quantities often leads to significant discounts.
- Look for Promotions: Take advantage of seasonal sales, manufacturer’s coupons, and closeout sales for major savings.
- Consider Used Equipment: High-quality second-hand equipment can be a cost-effective alternative if it’s been well maintained.
- Join Industry Associations: Membership in welding organizations may provide access to deals and exclusive discounts on supplies.
Assessing Value vs. Expense in Welding Gear
When evaluating welding supplies, it’s essential to consider their value beyond just the purchase price. Here’s how:
- Long-Term ROI: High-quality welding gear might cost more upfront but can lead to cost savings and better results over time.
- Performance Benefits: Investing in high-performance tools may improve productivity and efficiency on projects.
- Customization and Versatility: Equipments that serve multiple welding processes can reduce the need to buy additional machines, saving space and money.
- Safety Gains: The right safety gear diminishes the risk of workplace accidents, which can potentially save significant funds related to medical claims and downtime.