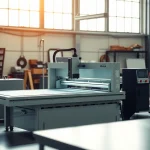
Introduction to Precision Die Cutting
Precision die cutting is a vital process in modern manufacturing that combines technology and technique to create high-quality, intricate designs from various materials. This method is essential for producing components used in several industries, ensuring that they are manufactured with exceptional accuracy and efficiency. As organizations increasingly demand sophisticated designs and customized solutions, understanding the nuances of precision die cutting becomes paramount. In this article, we delve into the definition, significance, applications, and the different techniques used in precision die cutting.
What is Precision Die Cutting?
Precision die cutting is defined as the process of utilizing a die to cut various materials into predetermined shapes, sizes, and designs with high accuracy. The die serves as a template and is usually crafted from hardened steel, making it sturdy enough to handle large volumes of production while maintaining the required tolerances.
Importance in Modern Manufacturing
The importance of precision die cutting in modern manufacturing cannot be overstated. It allows companies to achieve consistent results while reducing waste and production time. The precision with which components are made is crucial in industries such as automotive, electronics, and medical devices, where even the slightest deviation can lead to significant operational failures. Therefore, investing in high-quality die cutting services is essential for maintaining competitive advantages.
Common Applications Across Industries
Precision die cutting finds applications in numerous sectors. Here are some notable examples:
- Automotive Industry: Die-cut parts are used for gaskets, insulation, and seals to enhance vehicle performance and safety.
- Medical Field: Precision-cut materials are crucial in manufacturing items such as surgical instruments, bandages, and custom implants.
- Electronics: Components like circuit boards and insulation layers are often die-cut to meet rigorous standards for precision and reliability.
- Packaging: Brands employ die cutting for unique packaging designs that enhance user experience while promoting brand identity.
Types of Precision Die Cutting Techniques
Flatbed Die Cutting Explained
Flatbed die cutting involves using a flat surface where the material is placed, and a hydraulic press pushes down the die to cut through the material. This method is ideal for thicker materials and can handle multiple layers at once. While it is known for producing precise cuts, the setup time can be longer compared to other methods, especially for larger batches. However, it remains a favored technique for applications requiring high repeatability and detailing.
Rotary Die Cutting Advantages
Rotary die cutting employs a cylindrical die, which continuously spins to cut through materials. This technique is advantageous for high-speed production and is commonly used for materials such as paper, cardboard, and thin plastics. The primary advantages of rotary die cutting include:
- Speed: It allows for faster production rates compared to flatbed cutting.
- Flexibility: Capable of accommodating various material types and thicknesses.
- Precision: Produces clean, accurate cuts with minimal waste.
Comparing Laser Die Cutting
Laser die cutting uses a high-powered laser to cut materials with extreme precision. Unlike traditional methods, laser cutting does not require a physical die, which significantly reduces setup costs and time. The laser cuts with great accuracy, making this technique ideal for complex designs and smaller production runs. It also provides the capability to engrave or mark materials simultaneously, adding an extra layer of versatility, especially in branding applications.
Benefits of Using Precision Die Cutting
Cost-Effectiveness for Production Runs
One of the primary benefits of precision die cutting is its cost-effectiveness, particularly for larger production runs. While initially incurring a higher setup cost for creating the die, the cost-per-unit decreases substantially as production volumes increase. This economy of scale makes precision die cutting a preferred choice for manufacturers aiming to optimize their budgets without compromising on quality.
Consistency and Accuracy in Output
Precision die cutting enables manufacturers to achieve consistent product quality across large quantities. This uniformity is paramount in sectors such as automotive and medical, where strict compliance with regulations and specifications is mandatory. The high accuracy of die cutting reduces the possibility of defects, thereby enhancing operational efficiency and minimizing waste.
Flexibility with Various Materials
Die cutting is compatible with an extensive range of materials, including paper, plastic, rubber, and metals. This versatility allows manufacturers to innovate in product designs and develop customized solutions tailored to their specific needs. Whether producing intricate designs or standard shapes, the adaptability of precision die cutting caters to various market demands.
Choosing the Right Die Cutting Service
Factors to Consider in a Supplier
When selecting a precision die cutting service, several factors should be evaluated:
- Experience: Look for suppliers with a proven track record in the industry.
- Technology: Ensure they utilize modern and efficient technology to meet your production needs.
- Quality Assurance: Check for certifications and quality control processes in place.
Evaluating Technology and Capabilities
Different die cutting providers may have varying capabilities. It is essential to assess their machinery and technology to ensure they can handle your specific project requirements. Techniques like laser die cutting might be beneficial for intricate designs, while rotary die cutting may be more suited for high-volume output.
Understanding Turnaround Times and Pricing
Lastly, consider the supplier’s lead times and pricing structures. Understanding their typical turnaround times for different types of projects, as well as how pricing is calculated, can greatly impact your production schedule and overall costs. Requesting quotes and timelines upfront helps in making informed decisions and ensures alignment with your project deadlines.
Future Trends in Precision Die Cutting
Automation and Advancements in Technology
The future of precision die cutting is leaning toward increased automation. Advanced machinery equipped with online monitoring and data analytics is enhancing production workflows. This shift promises to optimize operations, reduce costs, and minimize human error, paving the way for even higher precision levels.
The Role of Sustainable Practices
As industries face pressure to adopt sustainable practices, the die cutting sector is no exception. Manufacturers are now seeking eco-friendly materials and processes that reduce waste and energy consumption. Utilizing recycled materials for die cutting can not only benefit the environment but also appeal to eco-conscious consumers.
Emerging Markets for Die Cutting Solutions
Emerging technologies and trends in consumer preferences are creating new markets for die cutting solutions. For instance, the rise of e-commerce has led to a demand for custom packaging solutions, while advancements in medical technology raise the need for precision die-cut surgical components. This evolving landscape presents opportunities for businesses that can adapt and innovate.